4月23日、旧カルソニックカンセイの重要な生産拠点で現マレリ・グループの中でも生産技術センターとして重きをなす吉見工場において、AJAJ勉強会が行われた。マレリは埼玉県では唯一1兆円超の売上高を誇る企業で、今回の機会には18名のAJAJ会員有志のみならず、埼玉県と国を代表する4名として公益財団法人 埼玉県産業振興公社 新産業振興部 次世代モビリティセンター埼玉 技術開発支援ループ コーディネーターの佐藤和浩氏、同公社の主任調査役の吉野一氏、埼玉県産業労働部 産業創造課 総務企画担当 主管の小黒慶教氏、経済産業省 関東経済産業局 航空宇宙・自動車産業室 係長の吉岡泰智氏も、参加した。
一同は吉見工場のスタッフの丁寧な誘導により、社員食堂の一角に迎えられた後、広報の清水氏、室井氏、保科氏や渉外の金井氏、工場長の尾崎氏、インテリア・イノベーションセンターの成富氏から、歓迎の挨拶が述べられた。AJAJを代表して菰田会長が謝意を述べ、和やかな雰囲気で勉強会はスタートした。
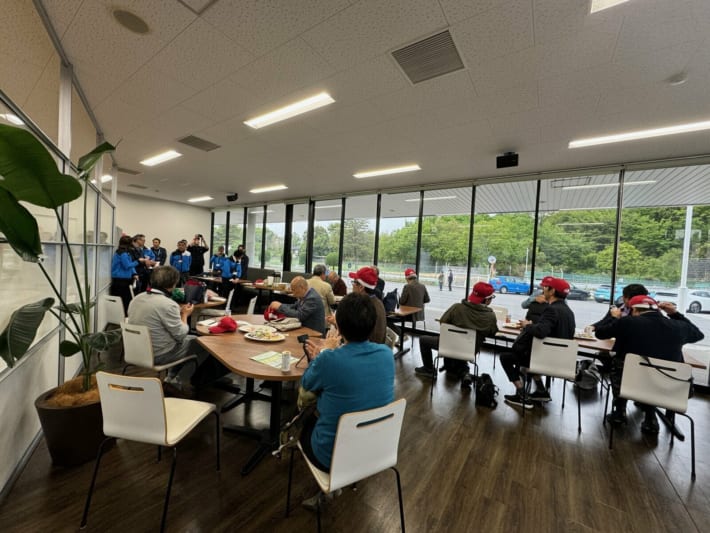
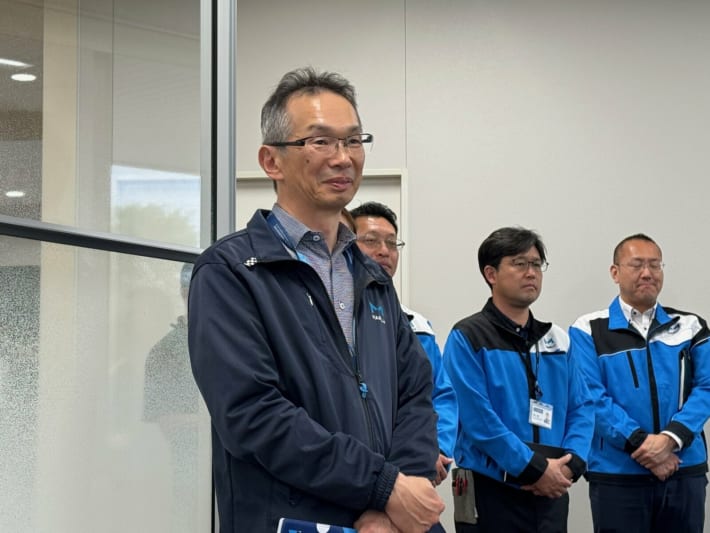
2グループに分かれ、イノベーションセンターと工場の生産ライン、それぞれから巡る流れで、筆者は前者のグループに入った。
インテリア・イノベーションセンターは昨年7月に開設され、ここ吉見に研究開発の全機能を集中させ、建物内にショールーム機能ももたせた。今後の開発の進め方の特徴となる「共創」をも視野に入れた造りだ。
「インテリアとエレクトロニクスがますます融合していく今、新しいイノベーションを作り出すことを目的に設置した施設です。領域の異なるエキスパートらが集まって、デジタルに沿った再現に基づいて生み出していくこと。色々な想像力やアイデアをいかに早く実現するか。そうしたマインドセットで取り組むことを始めたばかりです」と、担当者らは異口同音に述べる。
事実、現マレリ吉見のイノベーションDNAは、数多くの日本初、世界初を生み出してきた旧カルソニックカンセイの歴史でもある。時には立ち止まって観察すること、可視化することにも意味があり、OEMからデザイン業務を丸ごと委託されることもあれば、デザインと設計開発を一気通貫に手がけることもできる。
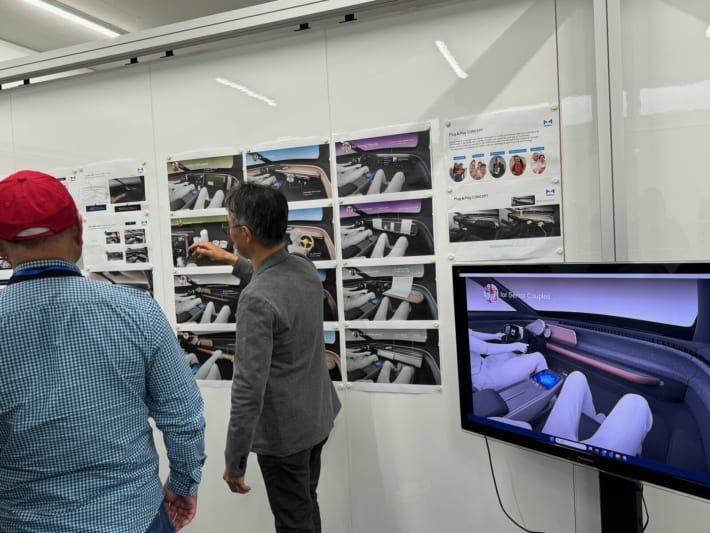
「ここはグローバルに市場ごとのキャビンデザイントレンドをベンチマークしているコーナーですね。平易にいえば、各市場ごとのインテリアの傾向を分析しながら何ができるかということです」
発表されたばかりの最新モデルのインテリアやダッシュボード周り、操作系など、そのアピアランスや機能を分析しながら、アメリカ、中国、欧州や日本、それぞれの顧客の求めるものは異なるという。その中から新しいものを、グローバルには共通モジュール化しつつ、スピーディに組み合わせていくという。
「今、世界的に共通しているのは、表示は遠くにワイドに、という点ですね。逆にいえば、ピラー・トゥ・ピラーで見せるのが行くとこまで行って、代わりにセンターコンソール近く、地図や触る部分が張り出してきています。そこでパッセンジャーの目の前が、スマートサーフェスまたはデコレーション化してきています。国産OEMのミディアムハイエンドでも、アメリカ市場ではフィジカルスイッチは多めですが、中国はフラッシュ化あるいはハイブリッド化を進めており、これらを組み合わせたものが主流になるでしょうね。プロジェクターも潜在性は高く、インターフェイスとの組み合わせも考えられます。高級車ほど間接照明も増えていまして、素材面が硬いプラスチックでも照明でコンソールの雰囲気、特徴を出す傾向にあります。またEVはフラットフロア構造ですから、コンソールのユーティリティはトレンドになると思います。サステナブルまたは再生可能素材は高価ですが、今後採用が進んでいくでしょう」
いわば、ここは社内で議論する場ながら、顧客にも足を運んでもらって共同で作業するスペースでもある。マレリとして顧客に何を提案できるか、マテリアルから仕上げのサンプル、それらを実装してインターフェイスごと確かめられるモックを見て触って体験してもらうこと。これを開発フローの上流とすることが、このショールーム機能を兼ねたイノベーションセンターの意義なのだ。
レザーのシート表皮ひとつとっても、様々なパターンのステッチやキルティング、またレザーのバリエーションとしてリンゴの芯や皮といった廃棄物を再生加工した、ヴィーガンレザーのようなサステナブルなものといった、各種サンプルがある。一方で照明の研究として、エモーショナル・バリューを上げるためのムードボードのサンプルもいくつか並べられている。
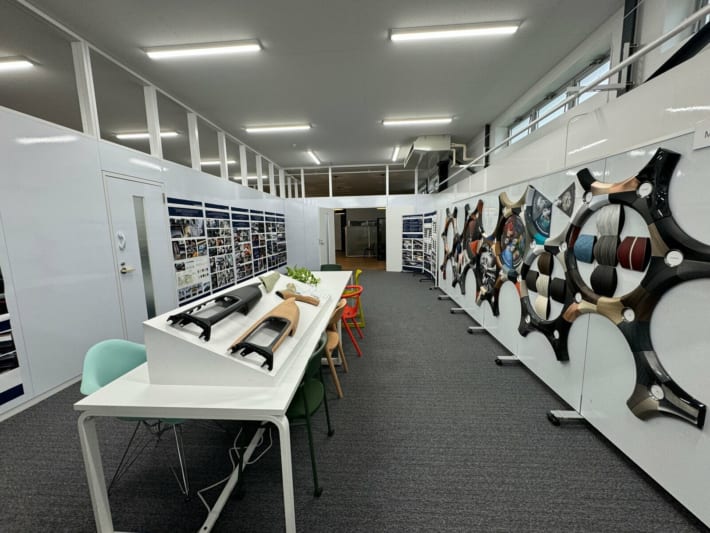
一方でインテリアとエレクトロニクスの先行開発コーナーでは、ディスプレイや加飾パネルなど、既存のアイテムについてもOEMからコストダウンが求められていく以上、マレリは号口同等以上で価値を高めるための技術を、多々用意している。金型と部品の間に塗料を流し込んで、模様や磨きのような仕上げを速く美しく実現する加工や、既存のメーターパネルと同じ価格で3倍以上のコントラストを実現するなど、下支えとなる技術の確かさが光る。加えて、ハードウェアに左右されずにデジタルやソフトウェア開発をスピーディに進めるためのデジタルツイン技術など、画面内の環境をクラウドで開発できる体制もある。
この日、イノベーションセンターには2024年CESで発表された「デジタルデトックス」が並べられていた。これは日常の暮らしで使うラウンジのように、自動車のキャビン内も寛げてヴァーサタイルな空間にすることができる、という提案型コンセプトだ。日本で研究開発して考えたものを、欧州に送ってさらに練り込み、実現のための部品やモジュールは中国で組み立てたという。
例えば、ホログラムのような近未来的かつ3D表示はドライバーの視界の正面もっとも近い位置にあり、AI活用が進めばインフォテイメント機能を動かすためのエージェントもしくはコンシェルジュ的存在として、車内インターフェイスをガラリと変える可能性がある。タッチスクリーンディスプレイの大画面化とゼロレイヤー化がいきつくところまでいった今は、むしろ情報をあれこれ大量に煩雑に表示し続けるよりも、必要な時に必要な情報を表示するだけでいいのではないか?という提案だ。だからラウンジのように質の高い内装マテリアルに囲まれながら、情報を隠すことも含め、必要な情報の提供の仕方をミニマムかつ豊富にしてあるというわけだ。
具体的には、ドライバーからほぼ同心円状に、走行情報からナビや音楽、ニュースに加え、手動走行中は見るべきではないエンターテイメント関連を表示する/隠す表示となっている。すべてのディスプレイをひとつのコントローラーで制御しているからこそ、乗員ごとに必要あるいは隠すべきもの、またはプライバシーに合わせて瞬時に情報を切り替えたり、スワイプひとつでエンタメのコンテンツを別の画面に転送することもできる。EVと自動運転が進む中で、ユーザーが車内でどう時間を過ごすか?というユースケースから出てきた考え方だ。実際、このプロトタイプはCセグのクロスオーバーのパッケージ・サイズに則っており、「デジタルデトックス」を名のってはいるが、同じぐらいかそれ以上に「デジタルアディクト」を求めるOEMも少なくないだろう。いわばマレリの側は素材も機能も最大限に近い選択幅を見せているわけで、OEMの側に実現したいインテリアのヴィジョン、編集的センスを求める話でもある。
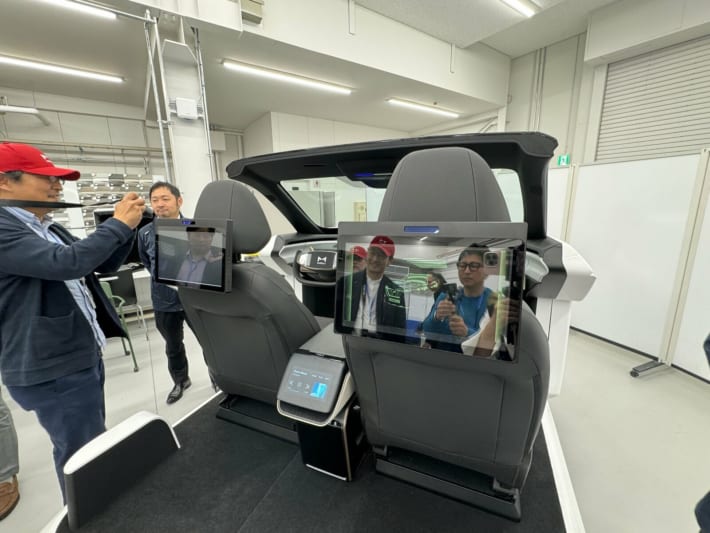
ここで勉強会の両グループが入れ替わり、後半は吉見工場のもっと伝統的な部分、生産ラインを見学していくことになった。
昨年2023年にビジネスユニットとしてインテリア・イノベーションセンターが合流し、吉見サイトでは今、約1150名の従業員を数え、うち工場では210名ほどが働いているという。生産する製品の96%がインテリアや内装部品で、2〜2.5トンのインジェクションモールドを備えた成型工場もある。ハイグロスなどペイント、モジュール組み込みやハプティックスイッチなどを、日産やトヨタの他にUDトラック向けに生産している。
実際、OEMの組立工場のラインでは車体に組みつけられるだけの状態で、コンソールやアッセンブリ、あるいはダッシュボードを丸ごと含むコクピットモジュールはほぼ、ここで組み立てられる。内装部品の他にも、ホンダ車のフロントバルクヘッドなどもライトやコンデンサなどを組みつけた状態で、送り出される。
塗装工程では最新の生産設備のひとつ、自己修復塗装の工程をまず訪れた。それまでにもシフトコンソール周りのパーツにピアノブラック塗装を2017年あたりから採用していて、生産開始当初は70%ぐらいで歩留まりが難しかったが、最終的には年93-94%にまで品質を安定させたという。そこへさらに難易度の高い自己修復塗装を手がけることになった。OEMからは自己修復塗装は70%もいかなくて苦戦するといわれたが、実際にスタートは66%だったという。それでもピアノブラックのときと同じように、目に見えないコンタミネーションを排除すること、除電を繰り返しては塗装に移ることを徹底した。マレリは手吹きのできる人材が多々いて、習熟度に応じて免許制にしているという。ロボットに動きを覚え込ませるにも、人の手のノウハウは要るのだ。
ロボットが動いている塗装ブースも、見せてもらった。ブース内の空気はダウンフローで、天井から風が当てられるなかでロボットが作動して樹脂成型されたパーツを塗る。その下には水で濡れたローラーが回っていて、つねに塗装溜まりができないようになっている。無論、こうした設定は環境配慮のため管理するにも有利だが、季節ごとに設定は微妙に最適化され、塗料の使用量をなるべく減じる方向という。
続いては成型ラインへ歩を進めた。成型機は大型3台を含む12台体制だ。日産車と繋がりは強いとはいえ、ホンダのステップワゴンやZR-Vのコクピットモジュールもここ成型棟で生産される。必要な部品を付けていく工程は、人の手でひとつづつ仕上げられていく。インサート成型であれば、部品をセットしてからロボットで金型を締めて、熱圧入するという工程もある。
最後に訪れたのは、GT-Rのダッシュボードにレザーやアルカンターラなどを張る工程だ。一人の熟練工が、成型されたダッシュボードに合わせて素材を当て、穴やスリットに合わせて細かな切り込みを入れては、徐々にフィットさせていく。1台分を生産するにも数時間、一日に今のところ数台というペースは、まさしく工房といった方がふさわしい。
最新鋭のデジタルからほとんど工芸的な生産手段まで、きわめて広いアプローチとノウハウそしてアイデアを自家薬籠中のものとしているからこそ、意図をもって車内空間を実現することがはじめて可能なのだ。
■参加者(18名) |
---|
会田肇/有元正存/石川真禱照/菰田潔/斎藤聡/鈴木直也/清水和夫/高山正寛/高橋アキラ/近田茂/南陽一浩/西村直人/松田秀士/森川オサム/諸星陽一/山崎元裕/吉田由美 |